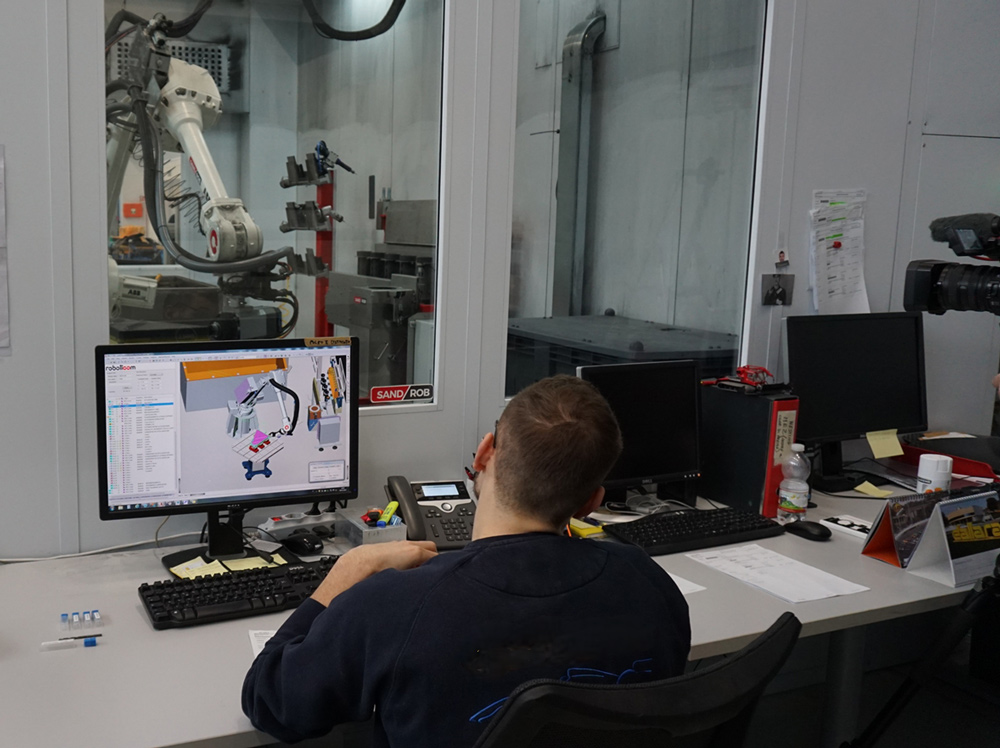
ROBOTIC PROGRAMMING BECOMES LIKE A GAME
ARPP® (Anthropomorphic Robot Production Planner) is Roboticom’s proprietary software designed to simplify and optimize the programming and control of robotic systems. Developed to be user-friendly and powerful, ARPP® ensures seamless integration and operation of robots across various industries, enhancing efficiency, precision, and flexibility.
Optimized Tool Paths
ARPP® generates optimized tool paths that enhance the precision and efficiency of robotic operations, reducing material waste and increasing productivity.
Simplified Programming
The software simplifies the programming process, allowing operators to quickly learn and implement robotic tasks without extensive training.
Seamless Integration
ARPP® integrates seamlessly with various robotic systems, ensuring compatibility and smooth operation across different applications and industries.
Real-Time Adjustments
With ARPP®, operators can make real-time adjustments to the robotic process, ensuring optimal performance and addressing any issues immediately.
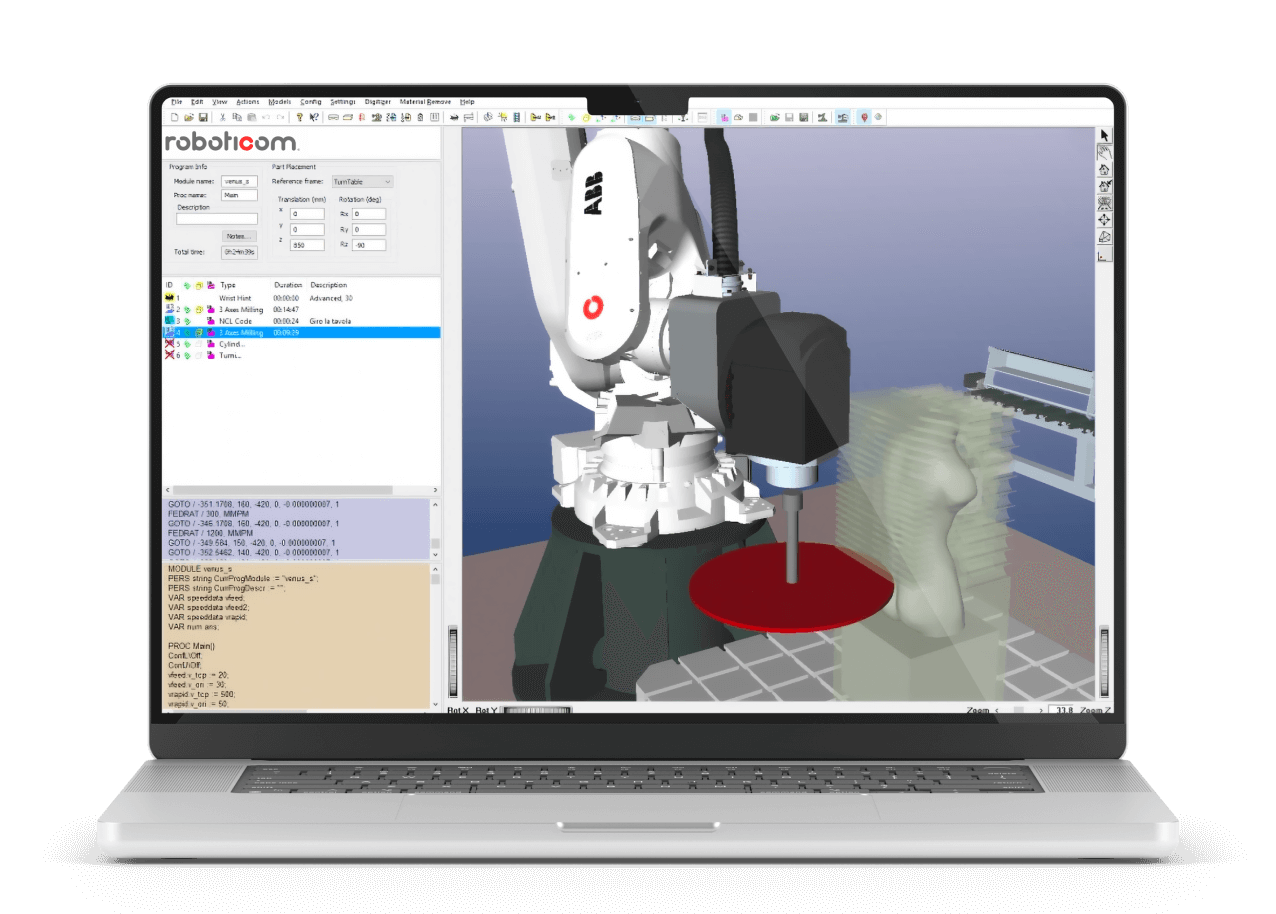
-
User-Friendly InterfaceARPP® offers a customized graphical interface that replicates the robot console, allowing users to control all processing parameters easily and functionally.
-
Comprehensive CAM FunctionalityThe software includes CAM functionalities that generate optimized tool paths for various processes, ensuring precise and efficient operations.
-
3D SimulationARPP® provides realistic 3D simulations of the material removal process, helping users visualize the robot's movements and actions in real time.
-
FlexRemote ApplicationThis feature allows for remote management and control of the robotic system, enabling real-time monitoring and data export, making it compliant with Industry 4.0 standards.
EASY-TO-USE, ALL-IN-ONE SOFTWARE
REAL-TIME DISPLAY OF MATERIALS REMOVAL
OUR PRODUCTS
CONTACT US
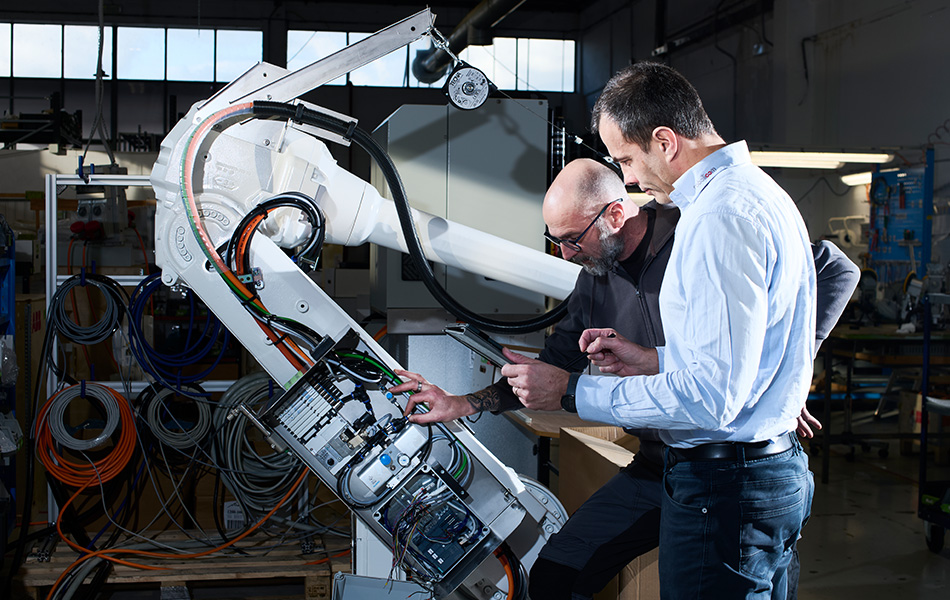