WHY CHOOSE ORTIS™?
Choosing Ortis™ for your orthopedic applications means leveraging state-of-the-art technology for superior milling and carving. Our robotic system offers unmatched precision, efficiency, and versatility. With successful installations in leading orthopedic facilities worldwide, Ortis™ has proven its ability to deliver consistent, high-quality results, ensuring the highest standards in patient-specific production.
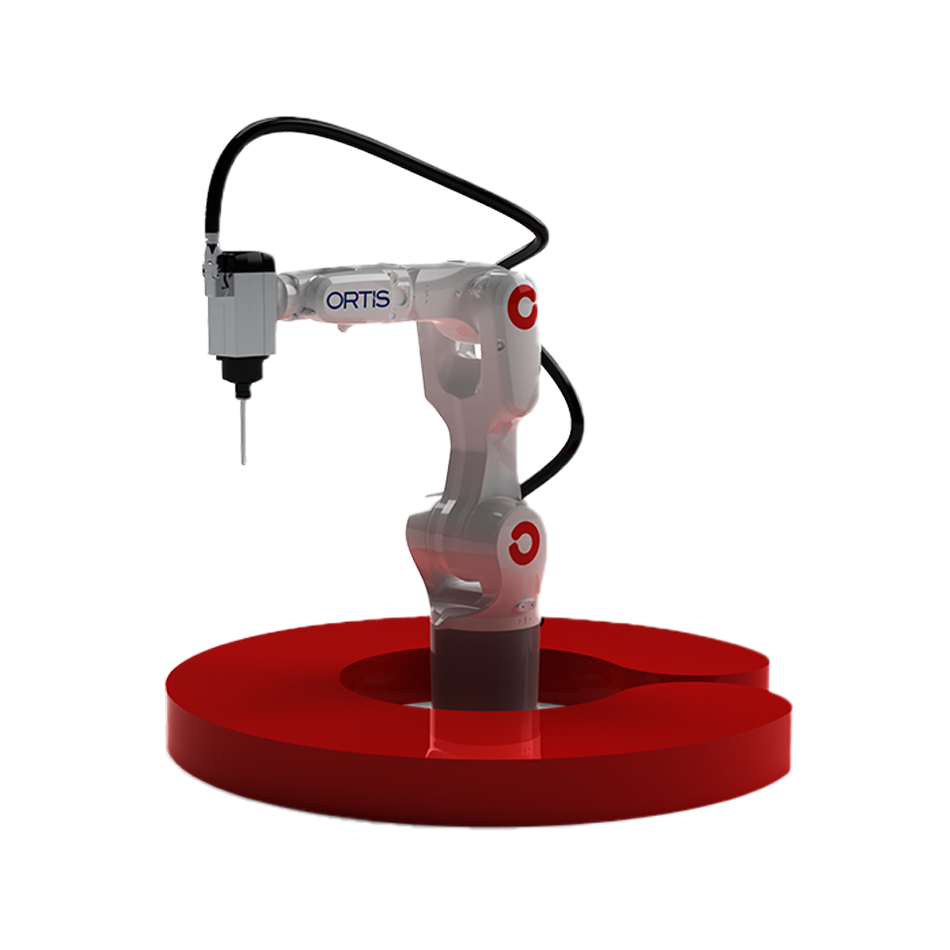
-
High PrecisionAchieve exacting standards with advanced control systems, crucial for custom prosthetic and orthotic devices.
-
Enhanced EfficiencyReduce production time and costs with automated processes tailored for orthopedic manufacturing.
-
Consistent QualityEnsure high-quality finishes with repeatable and reliable robotic performance, critical for patient-specific applications.
OPERATIONS
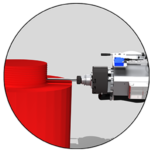
Carving
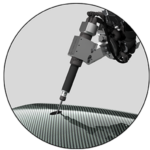
Trimming and Drilling
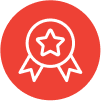
FEATURES
7-Axis Robotic System
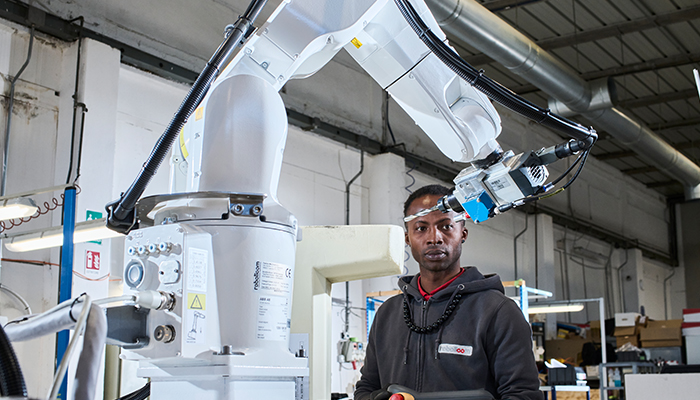
Combines a 6-axis robot with a coordinated rotary table actuated by a 7th axis.
Benefit: Enhances reachability across all areas of the workpiece, eliminating the need for repositioning.
Benefit: Enhances reachability across all areas of the workpiece, eliminating the need for repositioning.
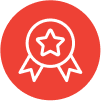
FEATURES
Easy Programming
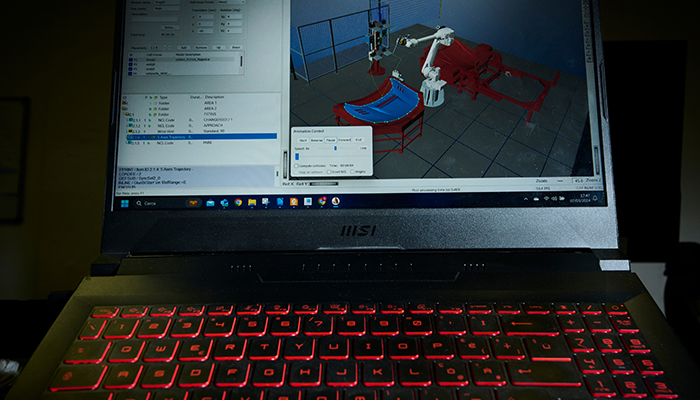
Features a fully integrated off-line programming software (ARPP) and on-line management software (RoMaS).
Benefit: Offers fast learning for machine programming and management, ensuring efficient and effective production.
Benefit: Offers fast learning for machine programming and management, ensuring efficient and effective production.
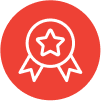
FEATURES
automated tool changing system
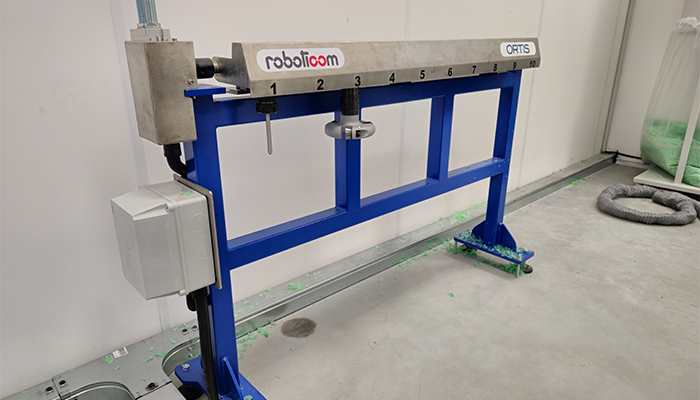
Automated system for switching tools during production.
Benefit: Minimizes downtime and ensures seamless operation during process changes.
Benefit: Minimizes downtime and ensures seamless operation during process changes.
ORTIS™ AT WORK
Ortis™ produces both positive and negative models for prostheses and orthoses, carves complex shapes with impeccable accuracy, carves plaster, soft foam, polyurethane and more, and automates tool change and speeds production.
MATERIALS
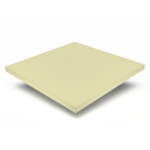
Polyurethane
Precise carving for custom orthotics and prosthetic components.
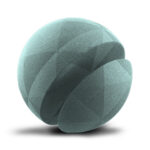
Soft Foam Rubber
Accurate carving for maximum comfort and support.

Plaster
Detailed carving for exact replicas and shaping.
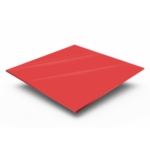
Plastic
Efficiently trim and drill components tailored to patient needs.
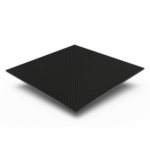
Composites
Tailored trimming and drilling to ensure fit of high-performance prosthetics.
ORTIS™ ESSENTIAL - Compact Size
Size
Small footprint
Capacity
Medium to low daily production volume
Right for
Perfect for small businesses getting started.
Small footprint
Capacity
Medium to low daily production volume
Right for
Perfect for small businesses getting started.
ORTIS™ PRO - Intermediate solution
Size
Medium footprint
Medium footprint
Capacity
Suitable for big size products and medium production volume
Right for
Workshops looking to expand production
ORTIS™ ENTERPRISE - Largest O&P Robot
Main Benefit
Automatic Tool Change, high productivity
Automatic Tool Change, high productivity
Right for
Expands production capacity
|
||||
ORTIS™ ESSENTIAL
|
ORTIS™ PRO
|
ORTIS™ ENTERPRISE
|
||
Robot Type | ABB 6-Axes 6 kg (13 lbs) Payload on the Wrist Working Area Approximately 1000 mm (3 feet) |
ABB 6-Axes or KUKA 6-Axes 20 kg (44 lbs) Payload on the Wrist Working Area Approximately 1600 mm (5 feet) |
ABB 6-Axes or KUKA 6-Axes 40-60 kg (88-132 Ibs) Payload on the Wrist Working Area from 2.000 to 2.500 mm (6 feet to 8 feet) |
|
380V Three-Phase Electro Spindle | 1.0 KW 24.000 rpm Auto Cooling System Up to ER20 Collect (Tool Shank Diameters from 2 to 12 mm) Manual Tool Change |
3.6 KW 24.000 rpm Fan-Cooling Up to ER30 Collect (Tool Shank Diameters from 3 to 20 mm) Manual Tool Change |
4.0 KW 24.000 rpm Fan-Cooling ISO30 Tool Holders (Tool Shank Diameters from 2 to 20 mm) Automatic Tool Change |
|
Presetting Laser | Laser Device Automatically Measures the Tool Length | Laser Device Automatically Measures the Tool Length | Laser Device Automatically Measures the Tool Length | |
Tool Box | 10-position toolbox for ISO30 Tool Holders The robot deposits the holder with the actual tool in the box and automatically takes the new required tool. | |||
Work Area | Processes blocks up to:
· Corsets – Diam. 600x(H)1000 mm · AFO / KAFO – 350x200x(H)650 mm · SEATING SYSTEMS – 500x600x(H)350 mm |
Processes blocks up to:
· Corsets – Diam 800x(H)1200 mm · AFO / KAFO – 350x300x(H)1000 mm · SEATING SYSTEMS – 800x800x(H)800 mm |
Processes blocks up to:
· Corsets – Diam 1200x(H)1500 mm · AFO / KAFO – 350x300x(H)1500 mm · SEATING SYSTEMS – 1200x1200x(H)1200 mm |
|
Dimensions | The Complete System: The Robot Controller is housed in an aluminum box, prearranged for chip suction. The dimensions are: 1700 length x 1250 width x 2450 height mm (6 feet length x 4 feet width x 8 feet height) |
Installation on Industrial Floor Minimum Area: 3000 x 3000 x 2700 mm (10 feet x 10 feet x 9 feet) Additional Area for Robot Control Unit: 1000 x 1000 x 2000 mm (3 feet x 3 feet x 7 feet) To increase the productivity, you can install more than one turntable/ xed table around the robot |
Installation on Industrial Floor Minimum Area: 4000 x 4000 x 3000 mm (13 feet x13 feet x 10 feet) Additional Area for Robot Control Unit: 1000 x 1000 x 2000 mm (3 feet x 3 feet x 7 feet) To increase the productivity, you can install more than one turntable/ xed table around the robot |
|
Weight | A total of about 600 kg (1300 Ibs) | Robot with its own base: 550 kg (1200 lbs) Turntable: 270 kg (600 lbs) Control unit: 250 kg (550 lbs) |
Robot with its own base: 650 kg (1500 lbs) * Turntable: 270 kg (600 lbs) Control Unit: 250 kg (550 lbs) Tool Box: 280 kg (625 lbs) |
|
Power Supply 380 VAC Three-Phase 50-60 Hz ** | 6 KVA (average consumption 1.5 KW) |
12 KVA (average consumption 4.5 KW) |
15 KVA (average consumption 5.5 KW) |
|
Noise Level | <75 dB | <75 dB on a typical installation | <75 dB on a typical installation | |
Compressed Air | Optional, at least 3 bar | Minimum 6 bar | Minimum 6 bar |
CONTACT US
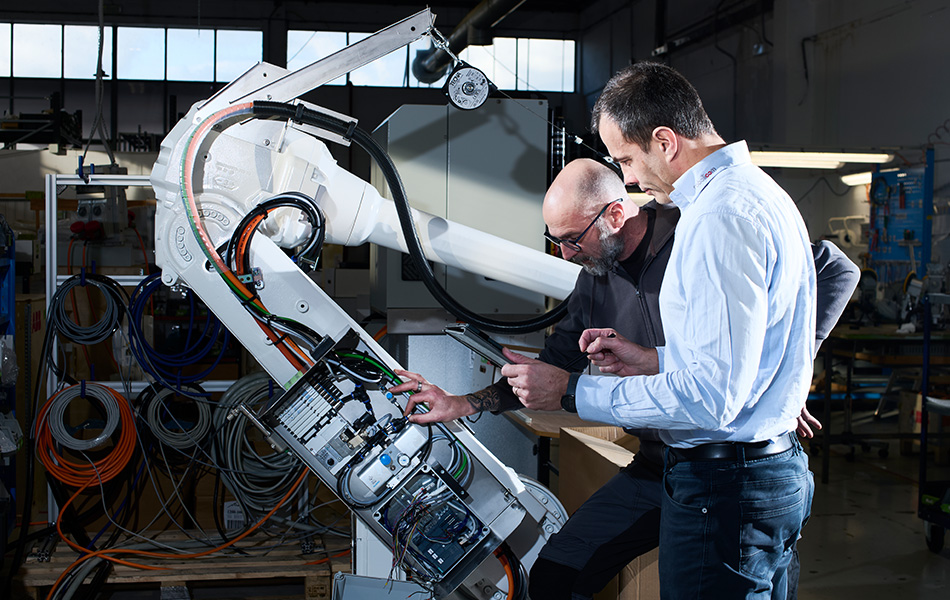